水溶性切削油管理の大切さ
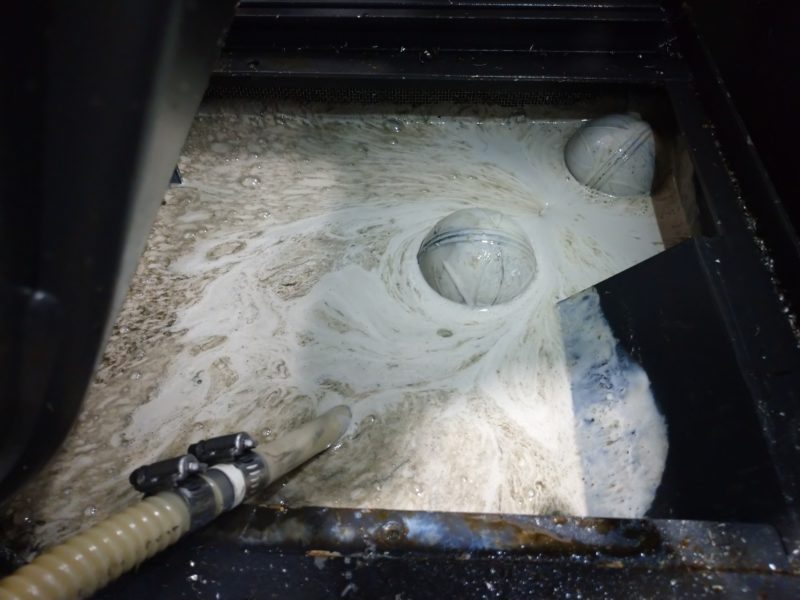
水溶性切削油の管理は濃度だけ管理していましたが、pH(水素イオン濃度)も管理し、浮上油回収装置を設置することで、悪臭・機械の汚れ・品質が全て改善されました。
改善前の状況
- 悪臭(特に休み明け)
- 製品のむしれ(特にアルミ)
- 機械内部の汚れ
- ホルダ・工具の汚れ
- タップ折れ
- 製品の錆(一番ひどかったのはA7075)
- クーラントフィルターの交換頻度が多い
改善することになったきっかけ
たびたび悪臭を指摘されていたが、その度に交換することはできないのである程度は仕方ないと考えていました。でもあまりに悪臭がひどくなると、急いでる仕事の加工中でも交換しないと体調を悪くする人も出てくるので、改善は急務となりました。
同時期にA7075の錆の問題、突然のタップ折れ、むしれも解決したいと言う理由も重なりました。
改善するために行った事
まず管理表をエクセルで作成し、継ぎ足しの前と後で濃度とpHを計測し記入。
切削油の状況が変化しすぎないように、タンクが半分くらい減ったら継ぎ足すようにしました。今まではMIN表示ギリギリで継ぎ足していました。
あと一番有効な改善方法として、浮上油回収装置を設置。
改善後の状況
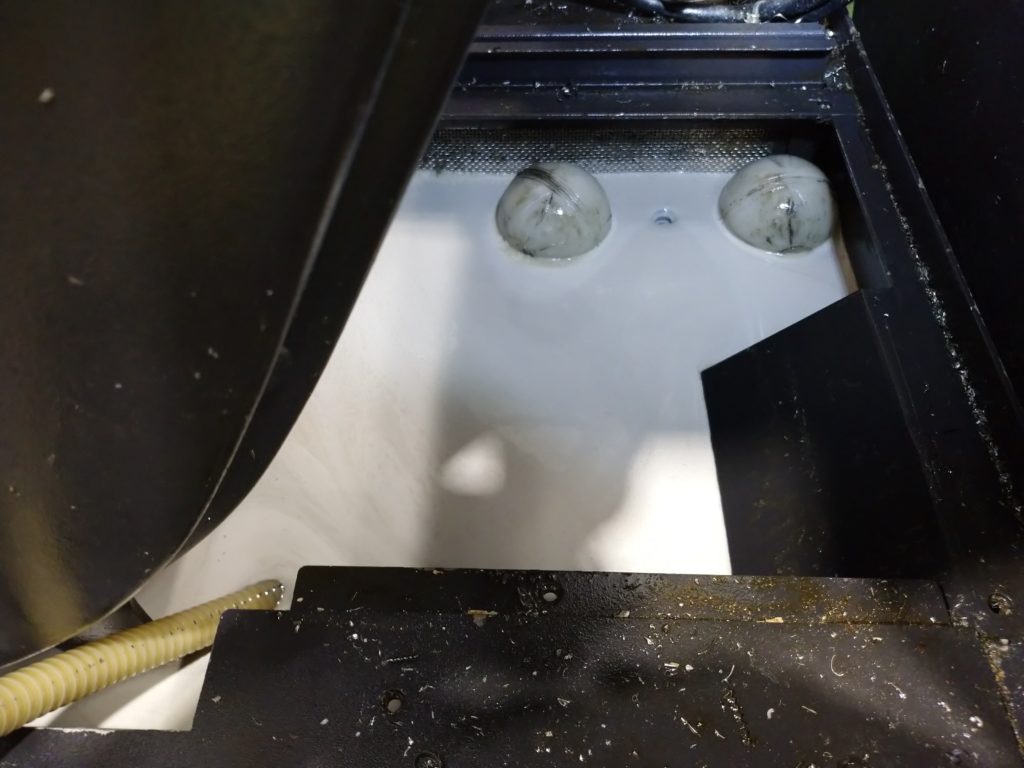
- ほぼ無臭
- 製品のむしれが無くなり、光沢が出る
- 機械内部の汚れが付かない
- ホルダ・工具も汚れ無し
- タップの折れ、激減
- 製品の錆、大幅に軽減
- クーラントフィルター交換頻度は少し改善
まとめ
やはり一番効果があったのは、浮上油回収装置です。こんなに改善されるならもっと早く導入すればよかったです。浮上油だけでなく浮上スラッジも回収できます。製品の不具合が減り、無駄なコストも減りました。浮上油回収装置への投資はすぐに回収できそうです。
みなさんも、工具がヘタる・折れる・綺麗に仕上がらない・錆びる・・・など。
工具や切削条件、加工方法を見直す前に、切削油改善で全て解決するかもですよ。